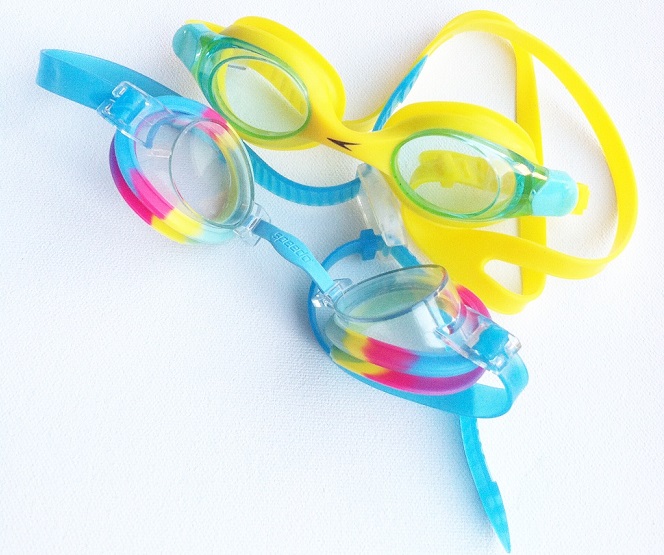
How does it work?
1. Waste rescue
The Econyl Reclaiming Program was set up by the Aquafil Group to recover Nylon 6 waste worldwide. The pre-consumer waste includes production waste, industrial plastic components and oligomers. The post-consumer waste includes fishing nets, fabrics and the fluff from carpet flooring. The collected waste is sent to a treatment center in Slovenia.2. Waste preparation
The materials are cleaned and prepared for depolymerization. As part of this process, materials other than Nylon 6 are removed and sent to other supply chains. The cleaned nylon waste is shredded and bagged.3. Depolymerization
The Aquafil Group has devised a technology that makes this chemical process less wasteful than any previous attempts, and as a result, less energy and water is used and less residual waste is created.4. Polymerization
Basically, the product that is created by this process (the Nylon 6 polymers) is identical to the product that is created using virgin materials.5. Transformation
The polymers created are distributed to the production facilities and processed into carpet flooring yarn and textile yarn.6. Re-commercialization
These products are then marketed to customers, like Speedo, around the world to produce their products.What else is Speedo doing to prioritize sustainability?
- Speedo is committed to continuing research into the water, waste and energy impacts of swimwear and goggle products.
- The company provides its designers and suppliers with the guidance necessary to avoid the use of any potentially harmful substances.
- The company considers the environmental impact when it sources packaging. For example, Speedo poolside footwear are displayed using lightweight, recycled card hangers instead of shoes boxes which saves approximately 18 tons of cardboard every year. The Speedo wristwatch packaging has been designed to be smaller and 88 percent lighter.
- All Speedo goggle packaging materials are certified as sustainable by the Forest Stewardship Council (FSC). And all goggle, footwear and swim cap packaging can now be recycled.
- Speedo also chooses to ship its products by sea or by road, instead of by air, whenever possible.
“Our priorities are to use less energy, to recycle more, and to use water and other natural resources responsibly.” – Speedo