Factory-made homes that move much like a family does have long had a reputation of being tacky, vinyl-sided shoe boxes on wheels. It’s a reputation that boutique prefab companies have been trying to change, according to a
Smart Money article.
Featuring the attempts of manufacturers to make an affordable, green alternative, it is true that many new features are for sale. A far cry from the old days of few choices, new sustainability-minded options for prefabs include bamboo floors, foam-insulated walls and energy-efficient kitchen appliances, among many other options.
Tempting consumers with choice, when putting features aside, it is helpful to remember some of the most popular selling points. Many are myths, according to
Chad Ludeman, President of Philadelphia-based postgreen
. Ludeman points out that from affordability to energy and materials conservation, prefab homes are stripped down to their basic components, and their subsequent lack of relevance in the affordable green-building world are revealed.
Myth 1: Prefab homes cost less money
The truth: Unless the building is being done in cities like New York or Los Angeles, a quality prefab home will cost more per square foot. Case in point: The standard price for a good prefab home with desirable features is at least $250 per square foot when all is said and done, according to Ludeman. In Philadelphia, the sixth largest city in the U.S., stick-built prices are only $125 to $150 per square foot, even with the more expensive labor involved. Hidden fees that cause the hike in prefab prices include facility overhead, crane charges, delivery setting and more. For all of the hassle, Ludeman says to build a home on the desired land and leave it there.
Myth 2: Prefab homes cause less waste because the factory reuses materials
The truth: Reuse and sustainability are not the focus of most companies, according to Ludeman. Compared to stick-house building, prefab homes actually use 20% to 30% more raw materials in order to withstand the transportation to the desired plot of land. There are plenty of programs that will recycle 90% of your construction waste — just ask the Construction Materials Recycling Association (CMRA), an organization that offers guidelines and suggestions. Representing an extensive group of member companies and agencies, CMRA keeps an eye on the recycling of 325 million tons of recoverable construction and demolition materials that are generated in the United States annually. These materials include aggregates such as concrete, asphalt, asphalt shingles, gypsum wallboard, wood and metals. The figures seem to suggest that if reuse and recycling are concerns, prefab isn’t necessarily the easy answer it appears to be at first glance.
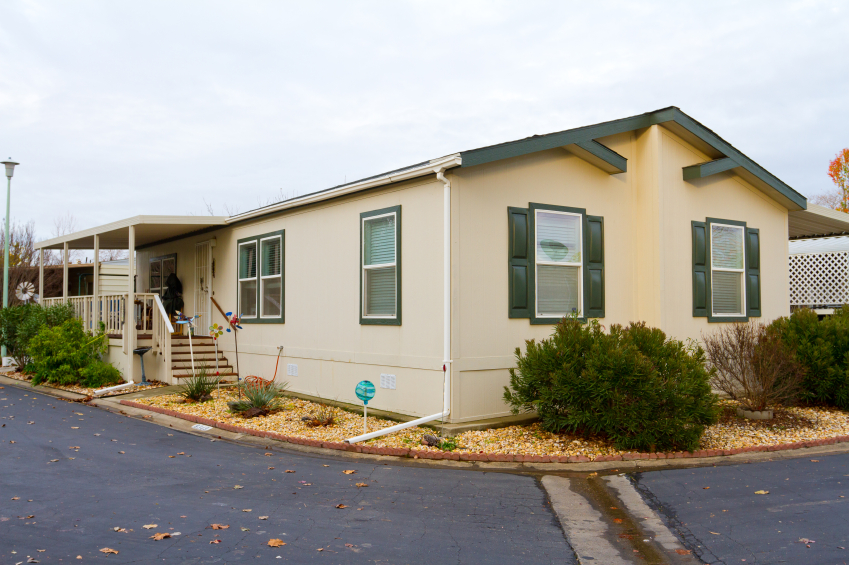
The truth: While many prefab homes are said to have insulation that is installed to better standards than site-built homes because of factory guidelines, the transportation of the home makes the insulation claims unlikely. According to Ludeman, most prefab companies still use loose batt insulation that falls out of the framing by the time it reaches the site. There is also much more to consider than batt insulation when it comes to energy efficiency. Ludeman put it this way: The more structural framing that connects to both the drywall inside and the exterior sheathing outside, the poorer the total insulation of the home. Most prefab homes boast a wood exterior, a very poor insulator. It seems that there are no shortcuts in the energy-saving efforts of consumers.
While prefab homes are still available, their pitfalls are much more public. Is there a right or wrong choice to be made? The facts seem to suggest that although prefab homes are not the quick, cheap and green answer that they promised to be a few years ago, they are still hanging on. That is, until America moves on.