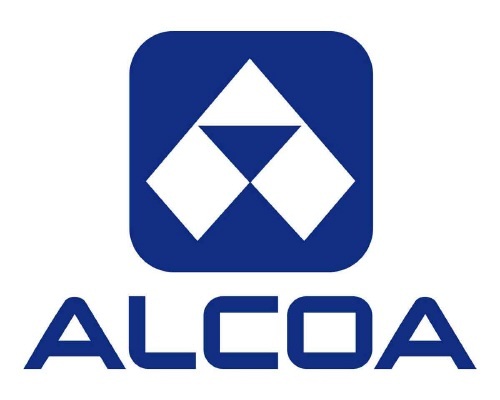
Alcoa Inc. is investing $21 million at its Barberton, Ohio, wheel-finishing plant to install an advanced recycling and casting process that will reduce energy consumption and greenhouse gas emissions.
The investment encompasses a 35,000-sq.-ft. structure at the company´s B&C Research facility that will use new technology to produce billet from remelted scrap aluminum. The aluminum billet will then be used to make new wheels, increasing the efficiency and sustainability of Alcoa´s manufacturing process, the company said.
“This project will strengthen Alcoa’s position as a technology leader,” said Tim Myers, president, Alcoa Wheel and Transportation Products.
The project will create 30 full-time jobs and help protect more than 350 existing positions, Alcoa said.
The Barberton plant is a machining and refinishing facility for commercial vehicle wheels made primarily at Alcoa’s plant in Cleveland. Aluminum produced at Barberton with the new process will be used at plants in Cleveland and Monterrey, Mexico, according to Alcoa.
Alcoa said using the new process reduces energy consumption by 25 percent.
This new process is another great example of Alcoa providing customers with innovative technology to make our 100-percent recyclable aluminum wheels even more efficient, while investing in the communities where we operate,” said Kevin Anton, Alcoa´s chief sustainability officer.
The expansion is scheduled to be completed the second half of 2012.
Source:
Tire Business